Product Design for Manufacture and Assembly 3rd Edition by Geoffrey Boothroyd, Peter Dewhurst, Winston Knight – Ebook PDF Instant Download/Delivery: 1040069487, 9781040069486
Full download Product Design for Manufacture and Assembly 3rd edition after payment
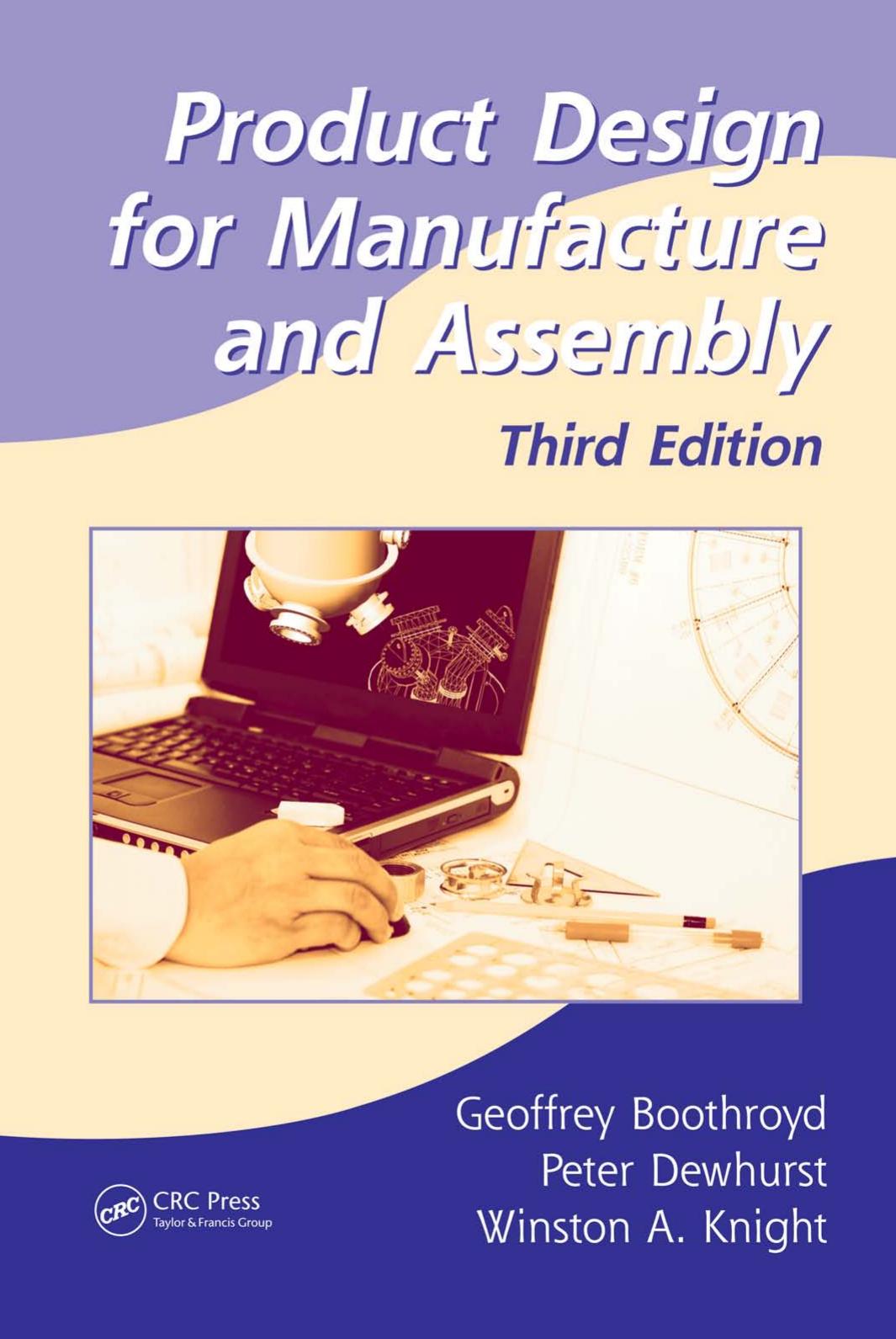
Product details:
ISBN 10: 1040069487
ISBN 13: 9781040069486
Author: Geoffrey Boothroyd, Peter Dewhurst, Winston Knight
Hailed as a groundbreaking and important textbook upon its initial publication, the latest iteration of Product Design for Manufacture and Assembly does not rest on those laurels. In addition to the expected updating of data in all chapters, this third edition has been revised to provide a top-notch textbook for university-level courses in product
Product Design for Manufacture and Assembly 3rd Table of contents:
1. Introduction
1.1 What Is Design for Manufacture and Assembly?
1.2 History
1.3 Implementation of Design for Assembly
1.4 Design for Manufacture
1.5 Producibility Guidelines
1.6 How Does DFMA Work?
1.7 Falsely Claimed Reasons for Not Implementing DFMA
-
1.7.1 No Time
-
1.7.2 Not Invented Here
-
1.7.3 Ugly Baby Syndrome
-
1.7.4 Low Assembly Costs
-
1.7.5 Low Volume
-
1.7.6 We Have Been Doing It for Years
-
1.7.7 It Is Only Value Analysis
-
1.7.8 DFMA Is Only One among Many Techniques
-
1.7.9 DFMA Leads to Products that are More Difficult to Service
-
1.7.10 I Prefer Design Rules
-
1.7.11 I Refuse to Use DFMA
1.8 What Are the Advantages of Applying DFMA during Product Design?
1.9 Overall Impact of DFMA on U.S. Industry
1.10 Conclusions
References
2. Selection of Materials and Processes
2.1 Introduction
2.2 General Requirements for Early Materials and Process Selection
-
2.2.1 Relationship to Process and Operations Planning
2.3 Selection of Manufacturing Processes
2.4 Process Capabilities
-
2.4.1 General Shape Attributes
-
2.4.2 DFA Compatibility Attributes
2.5 Selection of Materials
-
2.5.1 Grouping of Materials into Process-Compatible Classes
-
2.5.2 Material Selection by Membership Function Modification
-
2.5.3 Material Selection by Dimensionless Ranking
2.6 Primary Process/Material Selection
2.7 Systematic Selection of Processes and Materials
-
2.7.1 Computer-Based Primary Process/Material Selection
-
2.7.2 Expert Processing Sequence Selector
-
2.7.3 Economic Ranking of Processes
References
3. Product Design for Manual Assembly
3.1 Introduction
3.2 General Design Guidelines for Manual Assembly
-
3.2.1 Design Guidelines for Part Handling
-
3.2.2 Design Guidelines for Insertion and Fastening
3.3 Development of the Systematic Design for Assembly Methodology
3.4 Assembly Efficiency
3.5 Classification Systems
3.6 Effect of Part Symmetry on Handling Time
3.7 Effect of Part Thickness and Size on Handling Time
3.8 Effect of Weight on Handling Time
3.9 Parts Requiring Two Hands for Manipulation
3.10 Effects of Combinations of Factors
3.11 Effect of Symmetry for Parts That Severely Nest or Tangle and May Require Tweezers for Grasping and Manipulation
3.12 Effect of Chamfer Design on Insertion Operations
3.13 Estimation of Insertion Time
3.14 Avoiding Jams during Assembly
3.15 Reducing Disc-Assembly Problems
3.16 Effects of Obstructed Access and Restricted Vision on Insertion of Threaded Fasteners of Various Designs
3.17 Effects of Obstructed Access and Restricted Vision on Pop-Riveting Operations
3.18 Effects of Holding Down
3.19 Manual Assembly Database and Design Data Sheets
3.20 Application of the DFA Methodology
-
3.20.1 Results of the Analysis
3.21 Further Design Guidelines
3.22 Large Assemblies
3.23 Types of Manual Assembly Methods
3.24 Effect of Assembly Layout on Acquisition Times
3.25 Assembly Quality
3.26 Applying Learning Curves to the DFA Times
References
4. Electrical Connections and Wire Harness Assembly
4.1 Introduction
4.2 Wire or Cable Harness Assembly
4.3 Types of Electrical Connections
-
4.3.1 Solder Connections
-
4.3.2 Low-Pressure Connections
-
4.3.3 High-Pressure Connections
4.4 Types of Wires and Cables
4.5 Preparation and Assembly Times
-
4.5.1 Preparation
-
4.5.2 Assembly and Installation
-
4.5.3 Securing
-
4.5.4 Attachment
4.6 Analysis Method
-
4.6.1 Procedure
-
4.6.2 Case Study
References
5. Design for High-Speed Automatic Assembly and Robot Assembly
5.1 Introduction
5.2 Design of Parts for High-Speed Feeding and Orienting
5.3 Example
5.4 Additional Feeding Difficulties
5.5 High-Speed Automatic Insertion
5.6 Example
5.7 Analysis of an Assembly
5.8 General Rules for Product Design for Automation
5.9 Design of Parts for Feeding and Orienting
5.10 Summary of Design Rules for High-Speed Automatic Assembly
-
5.10.1 Rules for Product Design
-
5.10.2 Rules for the Design of Parts
5.11 Product Design for Robot Assembly
-
5.11.1 Summary of Design Rules for Robot Assembly
References
6. Printed Circuit Board Design for Manufacture and Assembly
6.1 Introduction
6.2 Design Sequence for Printed Circuit Boards
6.3 Types of Printed Circuit Boards
-
6.3.1 Number of Sides
-
6.3.2 Number of Layers
-
6.3.3 Board Materials
-
6.3.4 Device Types
-
6.3.5 Copper Weight
6.4 Bare Board Manufacture
-
6.4.1 Basic Bare Board Costs
-
6.4.2 Number of Boards per Panel
-
6.4.3 Hole Drilling
-
6.4.4 Optional Bare Board Processes
-
6.4.5 Bare Board Testing
6.5 Terminology
6.6 Assembly of Printed Circuit Boards
-
6.6.1 Assembly Operations for Through-Hole Printed Circuit Boards
-
6.6.1.1 Automatic Dual Inline Package Insertion
-
6.6.1.2 Automatic Axial (VCD) Insertion
-
6.6.1.3 Automatic Single Inline Package Insertion
-
6.6.1.4 Automatic Radial Component Insertion
-
6.6.1.5 Semiautomatic Insertion
-
6.6.1.6 Manual Insertion
-
6.6.1.7 Robot Insertion
-
6.6.1.8 Inspection and Rework
-
-
6.6.2 Assembly of Surface-Mounted Devices
-
6.6.3 Soldering Processes
-
6.6.3.1 Wave Soldering
-
6.6.3.2 Reflow Soldering
-
-
6.6.4 Other Assembly Processes
-
6.6.4.1 Cleaning
-
6.6.4.2 Rework
-
6.6.4.3 Board Testing
-
6.7 Estimation of PCB Assembly Costs
-
6.7.1 Component Insertion Costs
-
6.7.1.1 Insertion Cost
-
6.7.1.2 Setup Cost
-
6.7.1.3 Rework Cost
-
6.7.1.4 Programming Cost
-
-
6.7.2 Worksheet for Printed Circuit Board Assembly Costs
-
6.7.3 Example
6.8 Case Studies in PCB Assembly
-
6.8.1 Measuring Instrument Connector Board
-
6.8.2 Power Supply
6.9 Glossary of Terms
References
7. Design for Machining
7.1 Introduction
7.2 Machining Using Single-Point Cutting Tools
7.3 Machining Using Multipoint Tools
7.4 Machining Using Abrasive Wheels
7.5 Standardization
7.6 Choice of Work Material
7.7 Shape of Work Material
7.8 Machining Basic Component Shapes
-
7.8.1 Disc-Shaped Rotational Components (L/D ≤ 0.5)
-
7.8.2 Short, Cylindrical Components (0.5 < L/D ≤ 3)
-
7.8.3 Long, Cylindrical Rotational Components (L/D ≥ 3)
-
7.8.4 Nonrotational Components (A/B ≤ 3, A/C ≥ 4)
-
7.8.5 Long, Nonrotational Components (A/B > 3)
-
7.8.6 Cubic, Nonrotational Components (A/B < 3, A/C < 4)
7.9 Assembly of Components
7.10 Accuracy and Surface Finish
7.11 Summary of Design Guidelines
7.12 Cost Estimating for Machined Components
-
7.12.1 Material Cost
-
7.12.2 Machine Loading and Unloading
-
7.12.3 Other Nonproductive Costs
-
7.12.4 Handling between Machines
-
7.12.5 Material Type
-
7.12.6 Machining Costs
-
7.12.7 Tool Replacement Costs
-
7.12.8 Machining Data
-
7.12.9 Rough Grinding
-
7.12.10 Finish Grinding
-
7.12.11 Allowance for Grinding Wheel Wear
-
7.12.12 Allowance for Spark-Out
-
7.12.13 Examples
-
7.12.14 Machining Cost Estimating Worksheet
-
7.12.15 Approximate Cost Models for Machined Components
References
People also search for Product Design for Manufacture and Assembly 3rd :
7 product development process
z product
v design process
design for manufacturing and assembly examples
product design for manufacture and assembly geoffrey boothroyd
Tags: Geoffrey Boothroyd, Peter Dewhurst, Winston Knight, Product Design, Manufacture and Assembly